After years of being the darling of mid-rise European buildings and commercial projects in urban North America, cross-laminated timber (CLT) is starting to make its mark in a place you might not expect—single-family homes. And the results are nothing short of remarkable.
CLT is an engineered wood product made by gluing layers of dimensional lumber together in alternating directions. That simple concept creates something incredibly strong, incredibly precise, and surprisingly beautiful. Builders and architects are finding that CLT not only stands up to steel and concrete in terms of strength, but it also offers something those materials never could: the warmth and natural elegance of real wood, visible in walls, floors, and ceilings.
But CLT isn’t just a pretty face. The panels are fabricated in factories using CNC technology, meaning each one is cut with exact precision before it ever hits the job site. That allows homes to go up faster, fit tighter, and perform better—traits that matter a lot when labor is tight and quality expectations are high. For builders working with tight timelines, this level of offsite precision is a game-changer. For homeowners, it means better-built homes that look and feel like nothing else on the block.
Of course, people still have questions. Can CLT homes be built in hot climates? What about insulation and soundproofing? The short answer is yes, and then some. Wood does a decent job of insulating on its own, but most CLT homes today include additional insulation—often applied to the outside of the panels. Builders are using wood fiber, mineral wool, and other high-performance materials to meet or exceed energy codes in almost every climate zone. And when it comes to utilities, the factories can pre-cut chases for electrical, plumbing, and HVAC lines so the on-site crews aren’t hacking into the walls later.
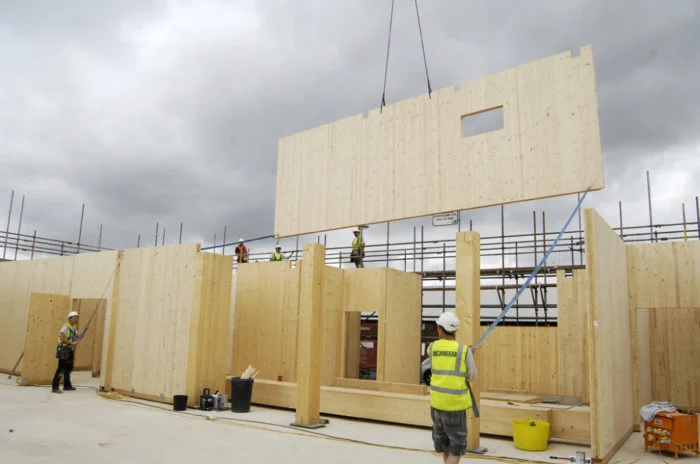
Even concerns about vibration and acoustics—issues that tend to pop up in lightweight wood systems—are being tackled head-on. Researchers at places like the University of British Columbia are running tests on how CLT performs under live loads, and some builders are experimenting with adding sand infill and hybrid steel connectors to reduce movement in high-traffic spaces. It’s not just experimental anymore—it’s practical, and it’s being done.
CLT may still be a bit more expensive than traditional stick framing, but the gap is closing. As more factories ramp up production and logistics improve, that cost difference will shrink. And for buyers who care about sustainability, carbon sequestration, and long-term durability, the investment in CLT is becoming easier to justify. These homes are not just green—they’re future-proof.
The best part? You don’t have to be building a ski lodge or a design-forward mansion to appreciate what CLT brings to the table. More architects are designing modest, affordable single-family homes using CLT in creative ways—sometimes leaving it exposed, sometimes covering it up, but always taking advantage of its unmatched strength and environmental benefits.
It’s taken a while for CLT to find its footing in the single-family space, but that time has clearly arrived. For those of us who’ve been following this material since it was a curiosity in a European trade journal, it’s exciting to see it finally showing up in backyards and neighborhoods here in the U.S. One panel at a time, CLT is building a future where homes are faster to build, smarter by design, and just a little more beautiful to live in.
.
With over 8,000 published articles on modular and offsite construction, Gary Fleisher remains one of the most trusted voices in the industry.
CLICK HERE to read the latest edition
Contact Gary Fleisher